How to guarantee safe pump start up operations by and avoiding dead-headed centrifugal pumps?
Guaranteeing safe pump startup operations
In many industries, pumps are an essential part of processes. Industrial pumps are used to move many different types of products, including water, chemicals, petroleum, wastewater, oil, sludge and slurry. Industrial pumps are designed specifically for use in harsh or heavy-duty applications. Still, they can be damaged as a result of incorrect valve operations during pump start-ups. Correct and safe pump start up operations are indispensable to guarantee a long life of pumps. avoid dangers and minimise plant downtime.
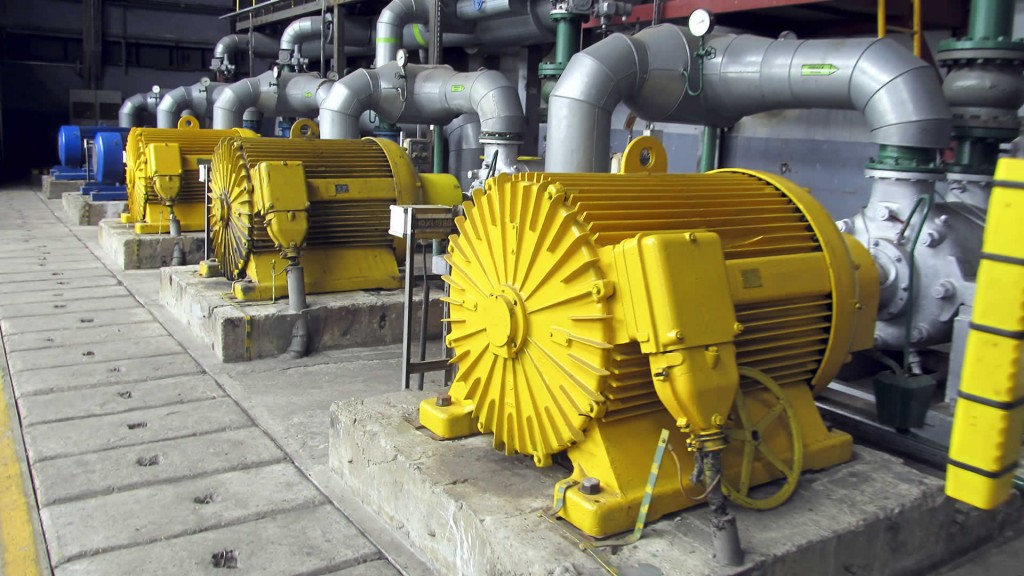
Dangers associated with pump start-up operations
A centrifugal pump is ‘dead-headed’ when it is operated with no flow through it, for example, with a closed discharge valve or against a seated check valve. If the discharge valve is closed and there is no other flow path available to the pump, the impeller will churn the same volume of liquid as it rotates in the pump casing. This will increase the temperature of the liquid (due to friction) in the pump casing to the point that it will flash to vapor. The vapor can interrupt the cooling flow to the pump’s packing and bearings, causing excessive wear and heat. If the pump is run in this condition for a significant amount of time, it will become damaged. Dead-heading can also lead to explosions, due to the energy being put into the liquid in the pump. Hydraulic overpressure and possible chemical reactions in the pump can also be caused by the overexertion of pressure.
Current risk mitigation attempts are inadequate
To protect the pump from running dead-headed one can provide a recirculation line from the pump discharge line upstream of the discharge valve, back to the pump’s supply source. The recirculation line should be sized to allow enough flow through the pump to prevent overheating and damage to the pump. Another way to be alerted of a dead head pump is to install a temperature sensor on the pump casing. This sensor will alert operators when the pump gets too hot and shut down the system as a precaution. Alerts can also be effected by installing a device that measures medium flow on the discharge line. If the water discharge has had a significant decrease, the device will alert of a possible blockage and shut off the system from potential damage. Unfortunately, a level sensor will not alert a dead-head pump situation.
Prevent dead-heading by enforcing safe pump line-up procedures
To eliminate the dangers of incorrect pump start-ups, Sofis offers an easy and effective solution. The main switch of the pump as well as the suction and discharge valve are equipped with valve interlocks. The operator must open both valves before he can turn on the main switch of the pump. The transfer of uniquely coded, linear keys from valve to valve, compel your operators to follow the correct pump start-up process steps and eliminate human error. Using interlocks, operators are only allowed to open or close the correct valve in the correct sequence, there is no bypassing the system.
Send an open or closed position signal to your control room
Optionally, the Sofis VPI position indicator can be used to indicate the right positions of the valves before the start-up or line-up procedure is started. VPI is a high-performance switch box for manual multiturn valves. It detects when valves have reached their open or closed position and sends a signal to your DCS. This valuable information about manual assets enriches your control system’s capabilities. It helps to further optimize your process performance, and prevents safety issues or damage caused by incorrect pump line-ups.
Using valve interlocks to prevent a pump dead-head; a practical example
To avoid a dead-head of the pump as a result of closed suction and discharge valves, you can deploy valve interlocks to enforce a predefined valve operation sequence. The valve operation sequence guarantees that the suction and discharge valves are opened first, before the power switch of the pump can be turned on.
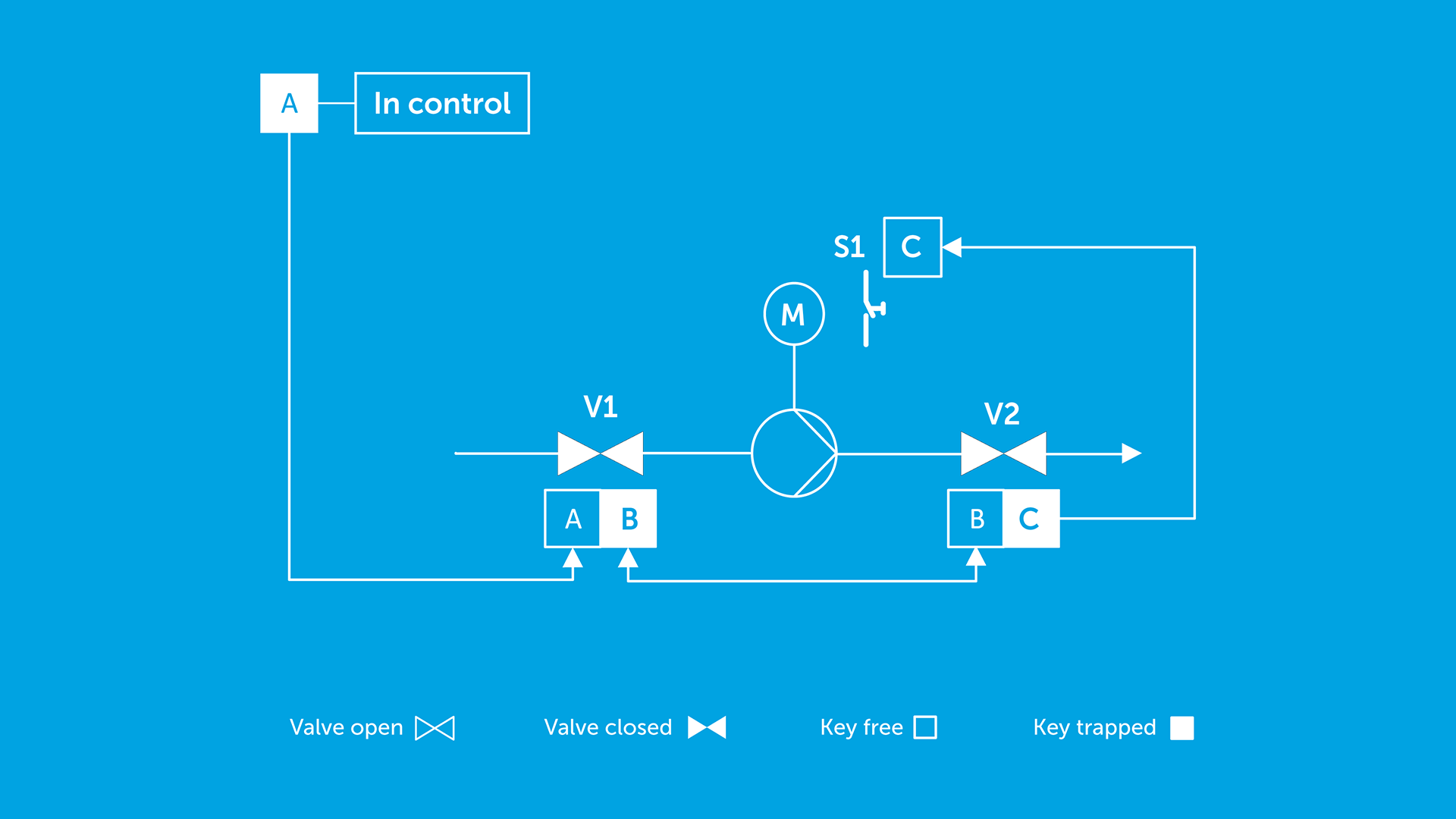
- Take Start Key A from the control room
- Insert Key A into the locking device of the suction valve (V1) of the pump. Open the valve and release Key B from the interlock. The valve is trapped in open position.
- Insert Key B into the locking device of the discharge valve (V2) of the pump. Open the valve and release Key B from the interlock. The valve is trapped in open position.
- Insert Key C into locking device of the main power switch (S1) of the pump and switch on.
The isolation of the pump will be done on the opposite way.