Maintain sufficient relief capacity during maintenance by safely isolating pressure relief valves.
Safely isolating pressure relief valves
Relief valves require regular maintenance and calibration. Plants install spare relief valves in their process systems to maintain sufficient relief capacity when a pressure relief valve is taken offline for maintenance. Switchover procedures require that the spare pressure relief valve is commissioned before any relief valve can be taken offline for maintenance.
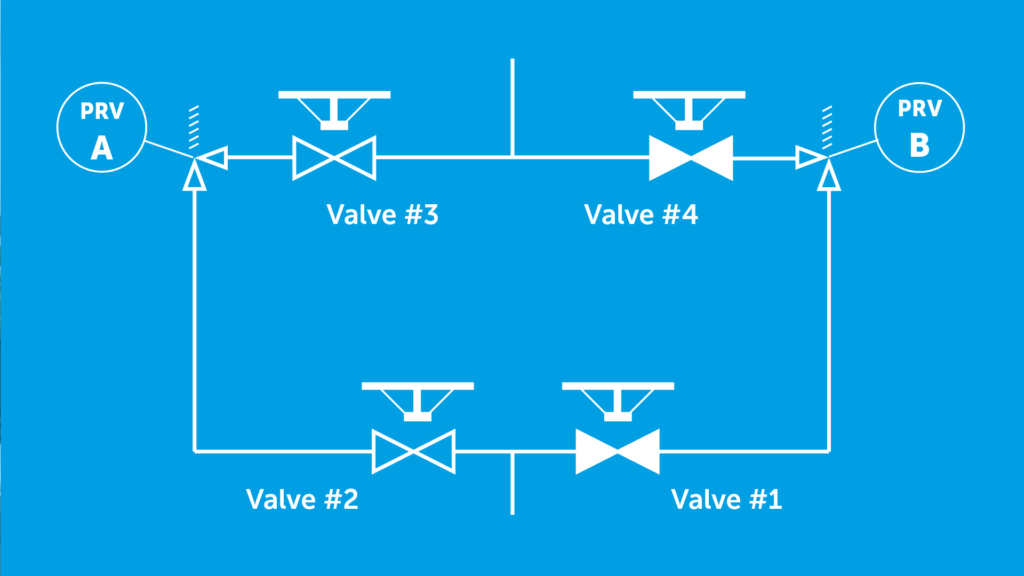
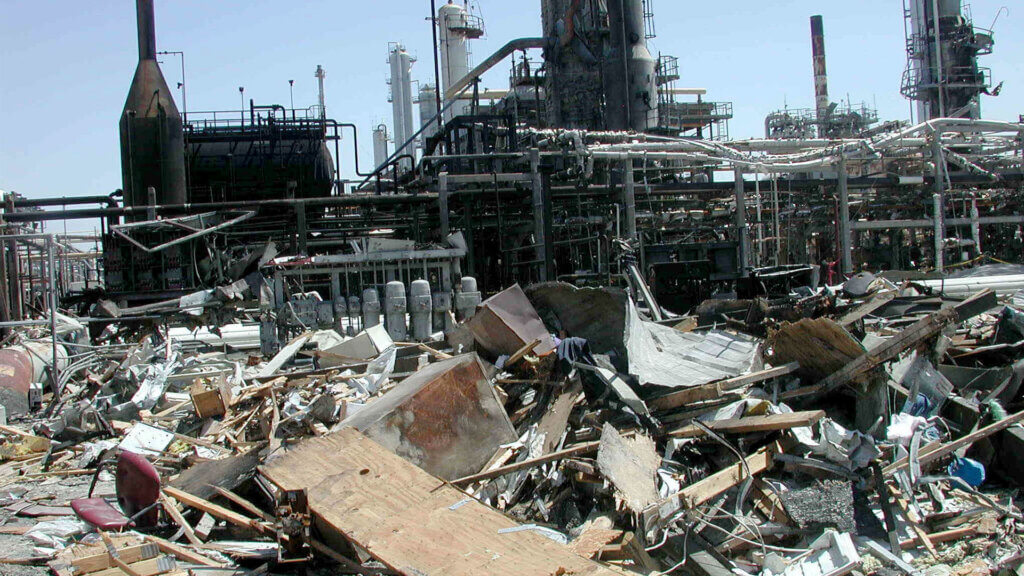
Dangers associated with maintenance
Pressure relief valves can be taken offline by closing isolation valves. These isolation valves are typically operated manually. Manual operations are prone to human error, leading to the following dangerous situations:
- When a pressure relief valve is removed for maintenance without being properly isolated, there can be a loss of containment causing environmental damage and massive risks of fires, explosions and poisoning of workers.
- Taking a relief valve offline before a spare valve is commissioned will lead to insufficient relief capacity. If an over-pressure event occurs while relief capacity is reduced, catastrophic consequences such as unplanned shutdowns, loss of production, spill, pollution, poisoning, fire, explosion, reputational damage, injury and death can become a reality. After the maintenance work is completed, the same situation can occur if valves are not re-commissioned correctly.
Current risk mitigation attempts are inadequate
Plants commonly mitigate these risks by implementing procedures, checklists, lockout-tagout, and other administrative controls. Such measures reduce the risk of human error, but do not completely remove it. In today’s modern workplace, adopting engineering controls to remove risk is the goal of every company.
Complete risk elimination is achievable
Sofis offers sequence control for manual valves without the need to actuate these valves. Our mechanical and digital valve sequencing systems guide operators through your pre-defined switchover procedures. They prevent human error by confirming that each isolation valve is operated in the correct order and stop operators who mistakenly deviate from procedures.
Once the switchover procedure is completed, our systems will provide your control room a visual confirmation of the valves status and a confirmation that sufficient relief capacity is online before maintenance activities can begin. This protects your plant and your operators from catastrophic consequences.
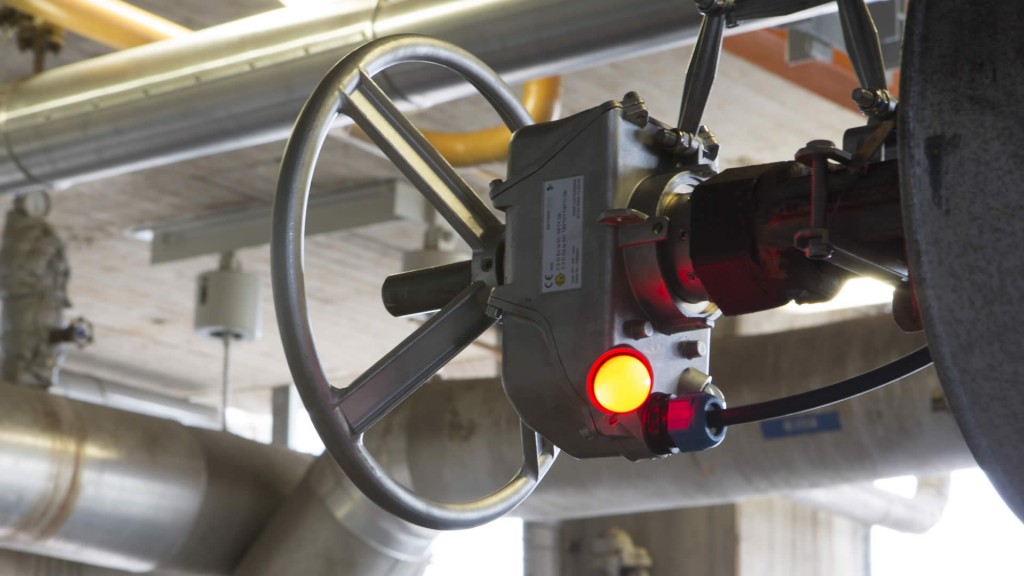
Avoid incorrectly blocked relief valves
Process plants have hundreds, if not thousands of pressure relief devices making up the most important active protection layer in their safety system. These devices need to be available at all times and under all circumstances. A simple human error could result in a closed isolation valve and a blocked path, effectively deactivating this vital safety system.
It’s difficult to track the position of all the isolation valves and unfortunately there are many cases where blocked paths have only been discovered after a catastrophic incident.
A custom made Sofis solution can easily be retrofitted to your plant to eliminate this risk. Sofis has protected over 350.000 valves worldwide from human error.