Hazard and Operability study
HAZOP
HAZOP, or a Hazard and Operability Study, is a systematic way to identify hazards in a work process. HAZOP is broken down into steps, and every variation in work parameters is considered for each step, to see what could go wrong. HAZOP’s approach is commonly used with chemical production and piping systems. Process facilities in the United States are required by OSHA to run a Process Hazard Analysis (PHA) every five years. Most commonly, a HAZOP is used to conduct the process hazard analysis.
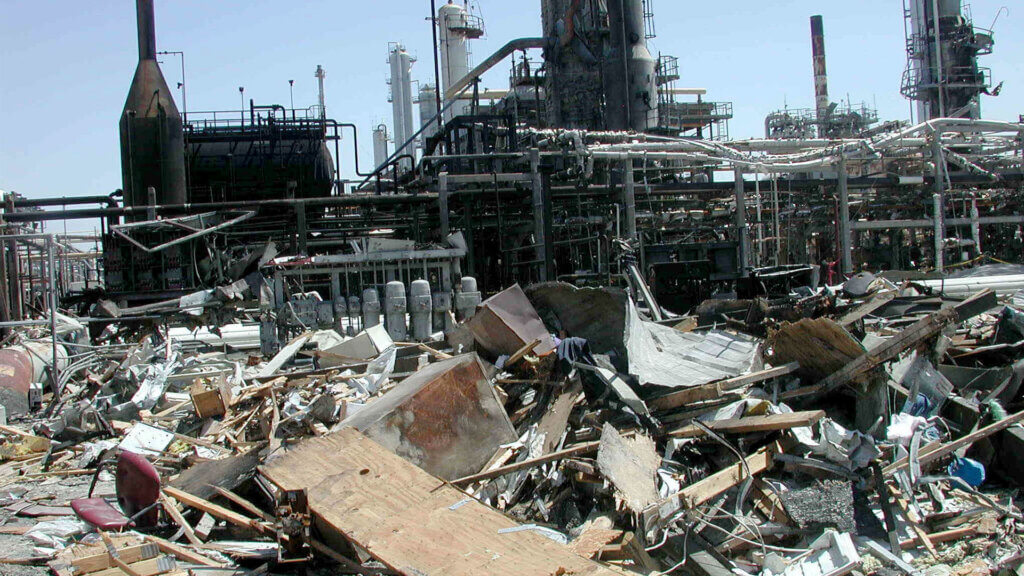
What is the aim of a HAZOP?
Major accident hazards and critical safety issues are inherent in the processes involved in refining, mining, chemical and other primary industries. Process safety risks can multiply across each process within a facility, and across every facility within a large national or multinational corporation. Even one small incident can lead to a more serious risk pathway developing as well. That’s why insurance companies, licensing authorities and government agencies, like OSHA, require Process Hazard Analysis (PHA) to identify, reduce and manage workplace hazards. One common method for PHAs is a Hazard and Operability study, better known as a HAZOP.
How to perform HAZOP?
HAZOP studies are performed when new facilities are built, when new processes are introduced or changes are made. They are also used to look at existing operation and maintenance processes. Typically, small teams of experts conduct the HAZOP, and then bring in an outside consultant to help facilitate the study. these teams will complete the study in four phases:
- Define the scope of the study.
- Prepare and collect necessary data.
- Examine the process and, using potential deviations, brainstorm causes of hazardous scenarios and their possible consequences to determine if they are significant.
- Document findings, make improvement recommendations and record any changes necessary to reduce risk.
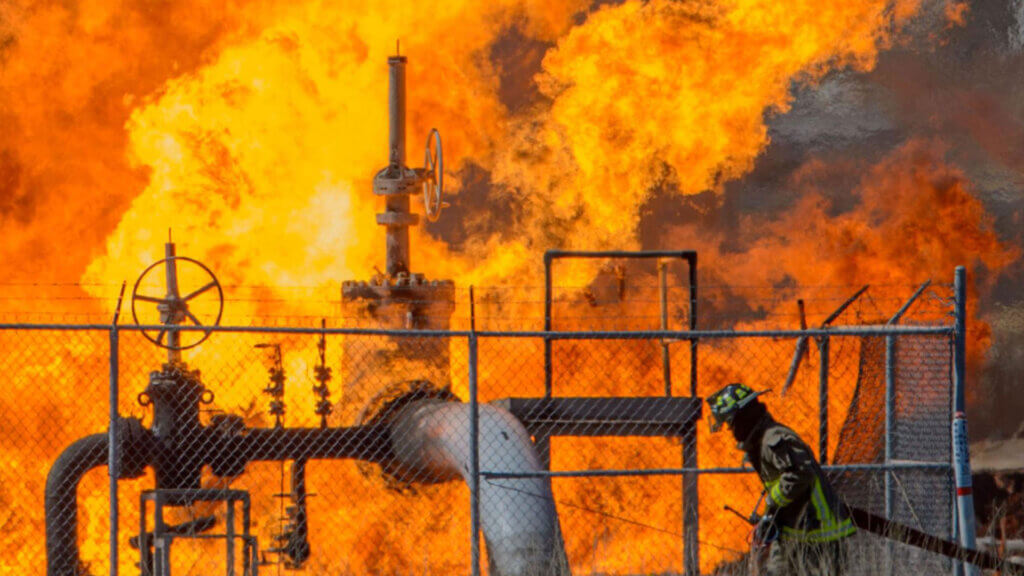
Why are companies adopting LOPA?
Process facilities in the United States are required by OSHA to run a Process Hazard Analysis (PHA) every five years. The most common tool used to conduct the process hazard analysis is a HAZOP. Process safety professionals have reported a trend for PHA’s to go one step further than a HAZOP, in a quantitative study of risk termed and many scenarios are pushed to a Layer of Protection Analysis, or LOPA. A LOPA study quantitively analyses the risk of an event occurring. Commonly, companies reference quantitative values for risk set out in the Initiating Events and Independent Protection Layer in Layer of Protection Analysis manual created by the Center for Chemical Process Safety. Most organizations have adopted this book as the standard for defining and quantifying risks in initiating events and will use this book for defining layers of protection.
Simplify manual valve operations
LOPA’s often leave teams with difficult task of trying to solve complex problems, without creating complex and expensive solutions. One very common example of this is trying to simplify a manual process without the complexity of full automating the process.
Applications where teams need to control the sequence of an operating valves in a manual process include that are identified in a LOPA are:
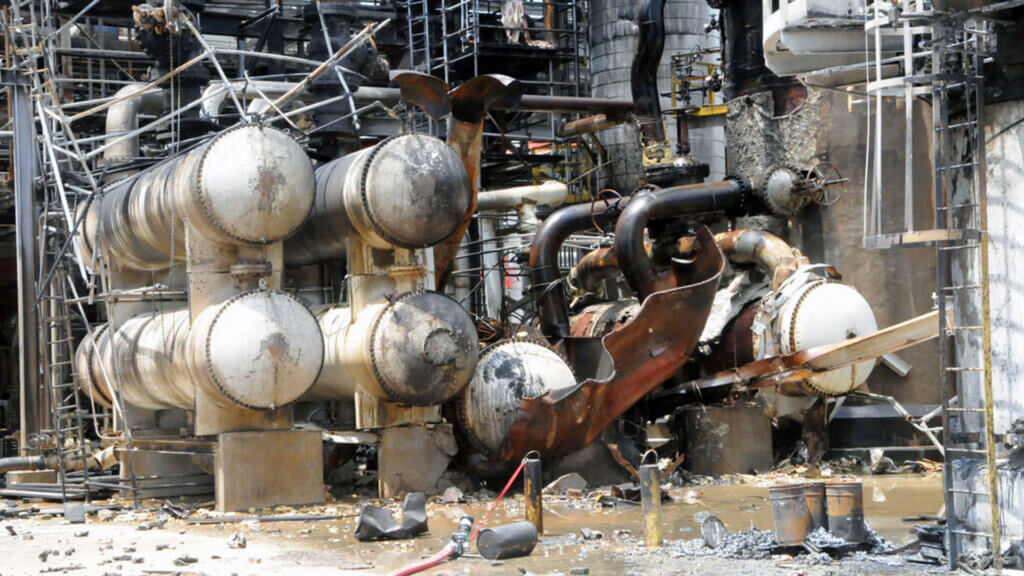
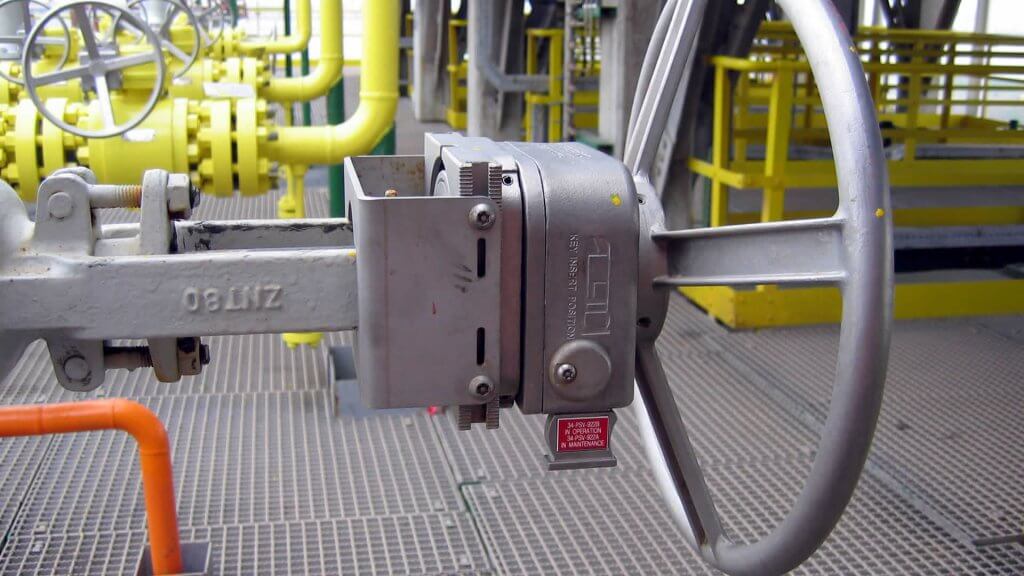
Using captive key systems to control manual valve operations
The most effective and simplistic solution for these complex scenarios lies on page 227 of the Initiating Events and Independent Protection Layers book, under the heading Captive Key. Captive key systems employ the use of locks that prevent the movement of valves and unique keys that will only be released in the desired valve sequence, preventing humans from operating valves in the incorrect sequence.
Achieve risk reduction by implementing captive key systems
The CCPS Guidelines subcommittee recommends that a Probability of Failure on Demand factor of .01 be awarded for Captive Key being used to controlling sequences. This means that systems that implement captive key can be awarded two credits or decrease the probability of an accident by a factor of 100. Captive key systems are a commonly thought of as a simple solution because they are retrofitted to the current system and require no adjustments for valves or equipment.
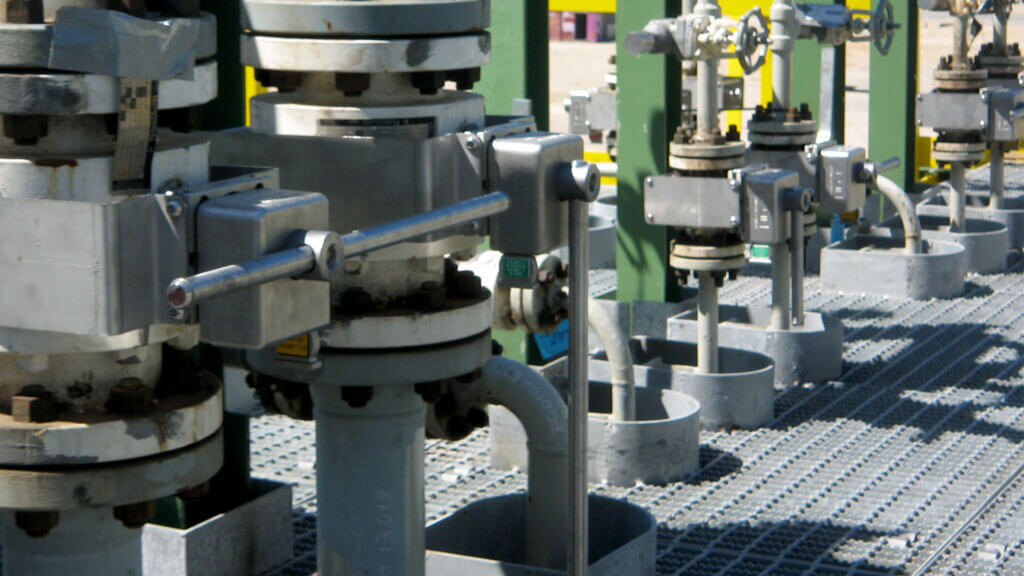
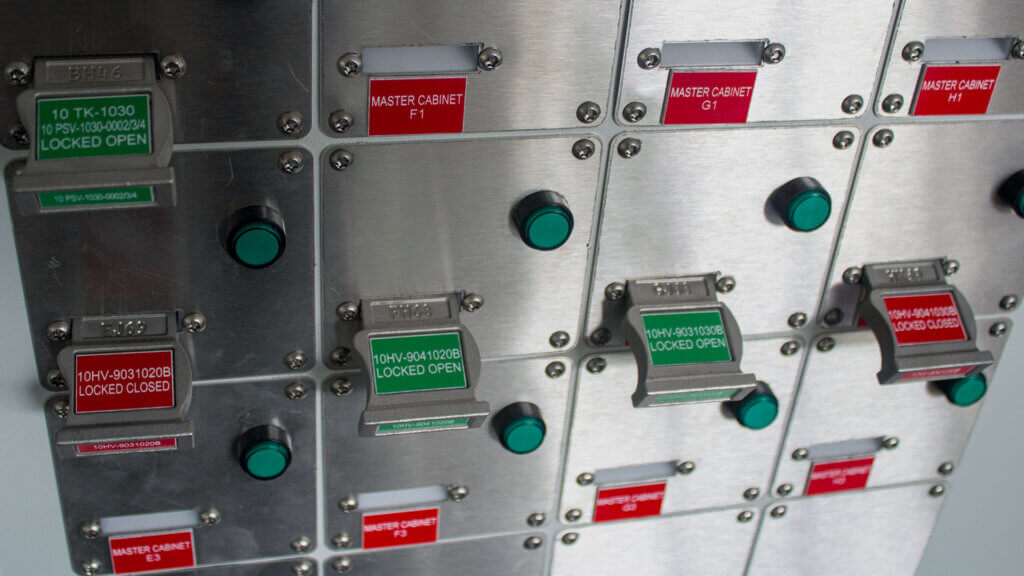
Download our whitepaper
Find out more on achieving risk reduction by implementing captive key systems!