How to avoid operators being exposed to dangerous levels of radiation?
Prevent dangerous exposure to radiation sources
Typically, valves are one of the controls used to regulate what is going on inside a process plant. Instrumentation however is vital to understand the conditions inside the process plant. Both valves as well as instrumentation are necessary to keep the plant running within its design parameters.
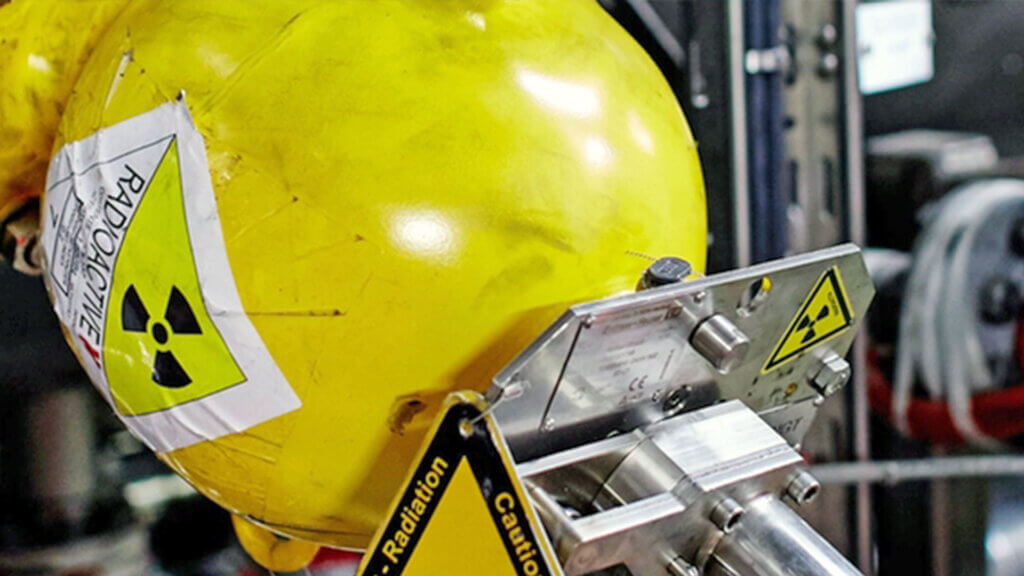
Using radiation sources to measure density and process levels
Instrumentation can take many forms, from simple sight glasses, pressure gauges and thermocouples to radar systems and systems utilising radiation sources. Gamma radiation is very penetrating and is scattered by dense materials. It is used for measuring the thickness of materials such as metals, detecting fill height or measuring density by detecting scattered radiation. By using penetrating gamma radiation, these measurements can be made through a vessel wall, so the instrumentation is not directly in contact with the process fluid. This is especially advantageous if the process conditions are aggressive or extreme in one, or more, ways. It also means the instrumentation is accessible without opening vessels or pipework.
Dangers of gamma radiation
Gamma radiation is invisible and can be deadly. In general, the higher the radiation dose, the sooner the effects will appear, and the higher the probability of death. When radiation collides with molecules in living cells it can damage them, causing a mutation. If the DNA in the nucleus of a cell is damaged, the cell may become cancerous. In this case the cell divides rapidly and causes serious health problems. The greater the dose of radiation a cell gets, the greater the chance that the cell will become cancerous. However, exceedingly high doses of radiation can kill the cell completely.
Securing ionising gamma radiation sources
Radiation sources should be properly marked, to indicate that they contain radioactive materials. The devices are lined with a lead shielding around the sealed source of radiation, which shields the environment from radiation. This shield should only be open when taking active measurements. The shield should be fully closed when the gauge is not in use. Workers usually receive little or no radiation from nuclear gauges due to the safety measures in place.
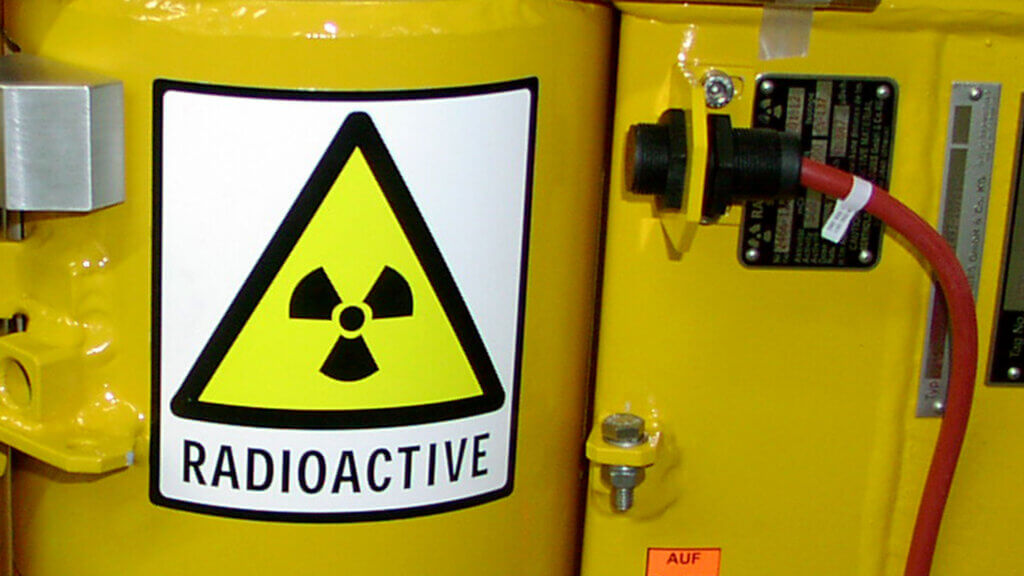
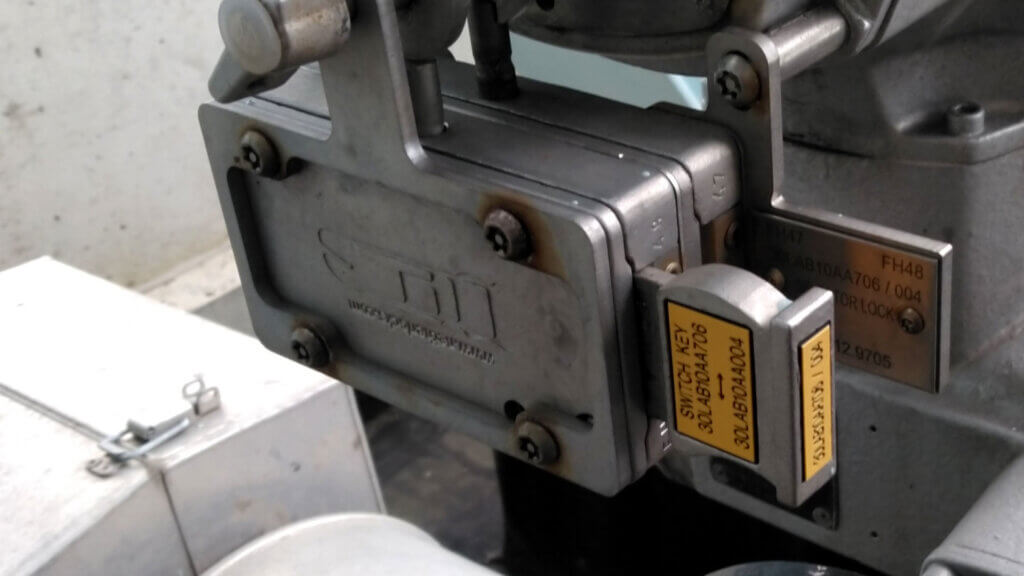
Using valve interlocks to prevent exposure to dangerous radiation
To guarantee that radiation sources will not expose operators to radiation, they can be incorporated into a system of valve interlocks. This can either be a single, simple device, operated by rotating a handle or lever, or by multiple sources, operated using pneumatic actuators. In both cases the sources can be secured, using mechanical valve interlock systems. The mechanical interlocks can also be interfaced with the plant’s electronic control system, to accept permissive signals from and to send status signals into the system where required.
Securing density gauges in LDPE units
Density gauges are used in both HDPE and LDPE (high density polyethylene and low density polyethylene) loop reactors. These gauges use radioactive sources to measure and monitor the density of chemicals. Systems consisting of interlocked radiation sources and interlocked valves can often be found on LPDE units. They allow a vessel to be isolated from the surrounding pipework and the radiation sources, before the access hatch to the vessel is unlocked for operator access to the inside of the vessel. This isolates the vessel from all pressure and chemical sources, as well as the invisible radiation beams from the instrumentation.
Securing reactor blow down vessels
Radioactive sources can also be found on reactor blow down vessels. During normal operation, the bottom closure (maintenance hole or door) of the reactor blow down vessel is closed. Safe opening and closing of the bottom closure can be effected by using valve interlocks. They guarantee that all isolation valves and radiation sources are fully closed, before opening the vessel for manual inspection and cleaning, and that the vessel is closed and all isolation valves and sources are opened again before restarting the plant. Typically, the valves are handwheel operated manual valves, and usually the sources are manually operated. However, it is also possible to interlock pneumatically actuated radiation sources. Electro-mechanical solutions also allow control system signals, like electrical signals like position indications, pressure, temperature, or other electrical signals, to be included into a mechanical valve operation sequence.
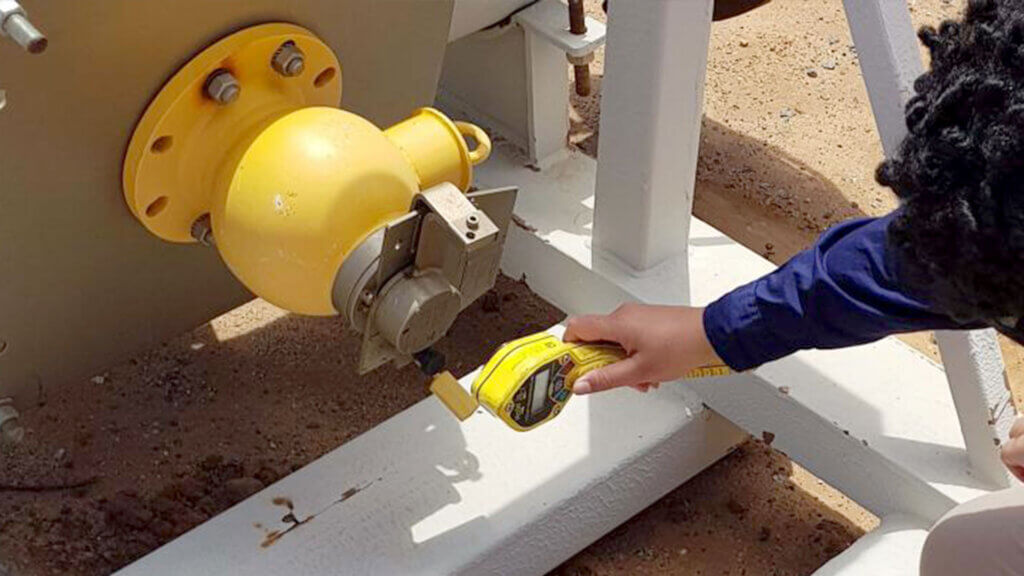
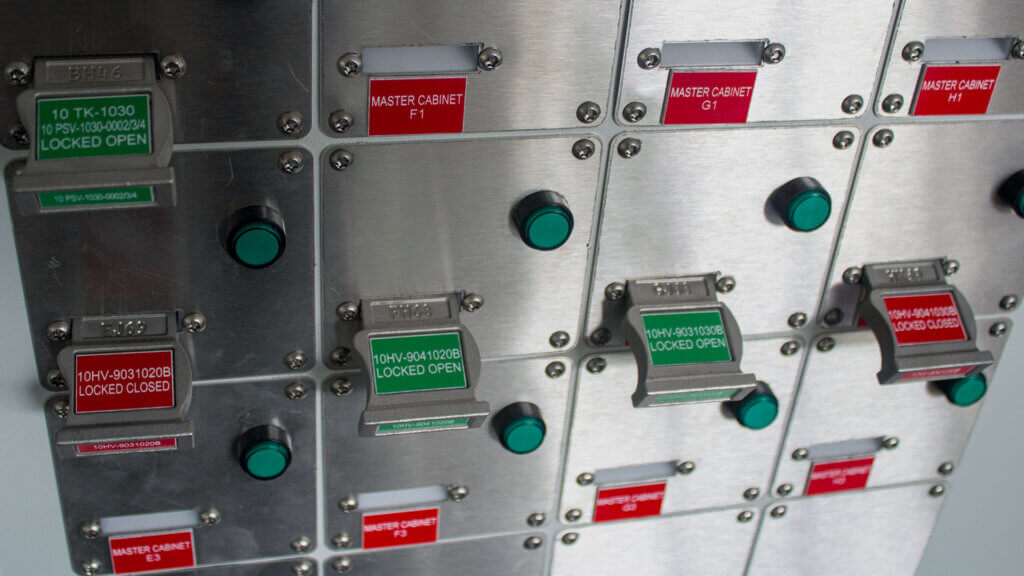
Safe access to a vessel dangerous levels of ionising radiation
Sofis has been supplying variations on valve interlocking systems for decades, both on the isolation valves and on the radiation sources. A comprehensive interlock system must be designed around the plant design, valves and radiation sources, as most systems vary in some way. Sofis has also cooperated closely with many radiation source OEM manufacturers over the years, to secure their equipment with valve interlock systems.
Creating a physical safety barrier
In the industry, companies review the plant safety standards on a regular basis, to comply with the latest regulations. In risks assessment exercises such as HAZOPs, PHAs and LOPAs, the risks per scenario can be reduced by either avoiding or mitigating the risk, to an acceptable level. As Sofis products create a physical barrier and provide administrative controls, the risk reduction can be awarded two points.